10 Common Commercial HVAC Issues and How to Address Them
- ETS
- Jan 25, 2024
- 5 min read
Updated: Jan 29, 2024
The HVAC system plays a pivotal role in maintaining a comfortable and efficient commercial space. It's the silent force behind a well-regulated environment, tirelessly working to ensure optimal temperatures and air quality.

However, this complex machinery is not immune to challenges. From subtle airflow issues to more noticeable malfunctions, commercial HVAC systems can encounter a range of common issues.
If left unaddressed, these issues can impact comfort, energy efficiency, and even workplace productivity.
We decided to make a list of 10 common commercial HVAC issues, shedding light on their causes, consequences, and strategies to effectively mitigate and prevent them from happening.
Understanding these common hurdles is the first step towards maintaining a seamlessly functioning HVAC system that stands resilient in the face of diverse operational demands.
10 Common Commercial HVAC Issues:

1. Poor Airflow
Causes:
Blocked or dirty air filters.
Issues with the blower motor.
Ductwork obstructions or leaks.
Consequences:
Uneven temperature distribution.
Reduced system efficiency.
The first step to take in managing and preventing poor airflow is routine inspection and maintenance of air filters.
Regularly replacing or cleaning filters prevents blockages and allows unrestricted airflow.
Additionally, thorough examination of the ductwork is essential. Any obstructions or leaks should be promptly identified and addressed to facilitate the smooth passage of air.
Ensuring the blower motor is functioning correctly is crucial, as it is responsible for the distribution of air throughout the system.
If poor airflow persists, collaborating with HVAC professionals for a comprehensive system evaluation is recommended.
Their expertise can pinpoint underlying issues such as improper system sizing or design flaws, allowing for strategic solutions to enhance airflow and restore the HVAC system's efficiency.

2. Refrigerant Leaks
Causes:
Wear and tear on components.
Corrosion in refrigerant lines.
Consequences:
Reduced cooling capacity.
Potential environmental impact.
Identifying the source of the leak through a thorough inspection of refrigerant lines and connections.
Once the leak is located, it's crucial to repair or replace the damaged components.
HVAC professionals should be engaged for this task, ensuring compliance with safety standards and regulations.
Following repairs, the system should undergo a recharge to restore the appropriate refrigerant levels.
Implementing regular preventive maintenance, including leak checks, and investing in quality installation practices can further mitigate the risk of refrigerant leaks, preserving the system's efficiency and minimizing environmental impact.

3. Thermostat Malfunctions
Causes:
Calibration issues.
Electrical problems.
Consequences:
Inaccurate temperature control.
System cycling problems.
Begin by checking the thermostat settings for accuracy, confirming that it reflects the desired temperature settings.
Calibrating or reprogramming the thermostat may be necessary to rectify any discrepancies.
If electrical issues are suspected, examining wiring and connections is crucial, and any damaged components should be repaired or replaced.
Upgrading to a programmable thermostat can enhance system efficiency and provide more advanced temperature control options.

4. Electrical Component Failures
Causes:
Overloading of electrical components.
Aging or worn-out wiring.
Consequences:
System shutdowns.
Increased risk of electrical fires.
Any signs of wear, damage, or overheating should be promptly addressed through repairs or replacements.
Regular preventive maintenance, including tightening loose connections and addressing minor issues, can significantly reduce the risk of electrical failures.
Implementing a proactive strategy that includes routine inspections, timely repairs, and collaboration with skilled professionals ensures the reliability and safety of the commercial HVAC system's electrical components.

5. Clogged or Dirty Coils
Causes:
Accumulation of dirt and debris.
Lack of regular maintenance.
Consequences:
Reduced heat exchange efficiency.
Increased energy consumption.
Addressing clogged or dirty coils in a commercial HVAC system is essential for maintaining optimal heat exchange efficiency.
Begin by regularly inspecting and cleaning the coils during routine maintenance.
Remove any accumulated dirt, debris, or contaminants using specialized coil cleaning solutions and soft brushes.
Ensure that the coil fins are straight and unobstructed to facilitate proper airflow.
In cases of severe contamination, professional coil cleaning services may be required to restore the coils to their optimal condition.

6. Water Leaks
Causes:
Condensate line blockages.
Malfunctioning drain pans.
Consequences:
Water damage to property.
Mold and mildew growth.
Start by identifying the source of the leak, which may stem from condensate line blockages or malfunctioning drain pans.
Clear any blockages in the condensate line and ensure proper drainage. Regularly inspect and clean drain pans to prevent overflow.
If leaks persist, engage HVAC professionals to conduct a thorough assessment.

7. Uneven Heating or Cooling
Causes:
Damaged or blocked ducts.
Imbalanced system output.
Consequences:
Discomfort for occupants.
Overworked components.
Assess and balance the distribution of air through the building's ductwork. Check for any obstructions or blockages that may impede the flow of conditioned air.
Adjusting dampers and registers can help redirect airflow to areas with temperature disparities.
Additionally, consider upgrading to zoning systems that allow for customized temperature control in different zones, optimizing comfort and energy efficiency.
Regular maintenance, including cleaning vents and inspecting ductwork for leaks, is vital for preventing airflow restrictions that contribute to uneven temperature distribution.

8. Frozen Evaporator or Condenser Coils
Causes:
Insufficient airflow.
Low refrigerant levels.
Consequences:
Reduced system efficiency.
Potential damage to compressor.
The root cause of the freezing may include issues such as inadequate airflow, low refrigerant levels, or dirty coils.
Thawing the coils is necessary, which can be achieved by turning off the system and allowing the ice to melt naturally or using a controlled heat source.
Once thawed, address the underlying issues by replacing dirty filters, fixing airflow restrictions, and ensuring proper refrigerant levels.

9. Strange Noises
Causes:
Loose or damaged components.
Unbalanced fan blades.
Consequences:
Disruption in the workplace.
Indicates potential issues.
The source of the sounds could range from rattling ductwork to loose components. Tighten any loose screws or bolts and ensure that fan blades are balanced.
If the noise persists, inspect the blower motor, compressor, and other moving parts for signs of wear or damage.
Lubricating moving components can sometimes alleviate friction-related noises.
Regularly scheduled maintenance, including inspections and component lubrication, helps prevent unusual sounds and ensures smooth system operation.
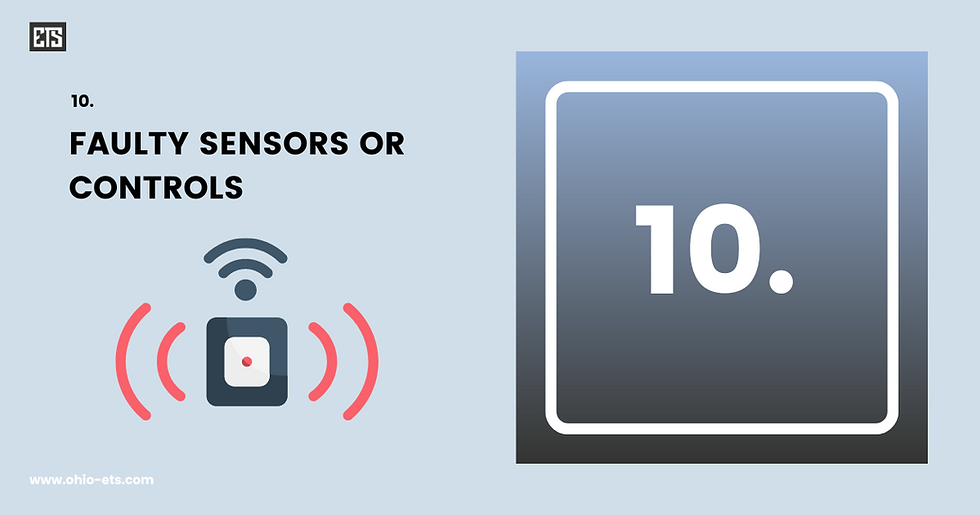
10. Faulty Sensors or Controls
Causes:
Sensor calibration problems.
Electrical issues in control systems.
Consequences:
Inaccurate temperature readings.
Poor system performance.
Checking and calibrating the sensors to ensure accurate temperature readings is a good place to start.
Verify the electrical connections and wiring for any signs of damage or loose connections. If you continue to have problems, consider reprogramming or replacing the faulty sensors.
Similarly, inspect control systems for any malfunctions, addressing electrical or programming issues promptly.
Conclusion
Regular maintenance, timely repairs, and proactive troubleshooting can help address and prevent these common issues, ensuring the reliable and efficient operation of a commercial HVAC system.
If you are looking for help with your commercial HVAC system and are located in the Columbus, Ohio area, be sure to contact ETS.
Avoid an expensive repair or unexpected replacement by getting year-round protection with a preventative maintenance care plan for your heating & cooling system.
Want more articles like this one? Check out the ETS blog!
Comments